Component production
Tailor-made solutions
Our component production conforms to the highest standards. Innovative production technologies, state-of-the-art machines and qualified employees produce premium quality from the smallest to the largest component.
Bildergalerie aus der Produktion
Komponentenfertigung
Machining
We can draw on decades of experience in the production of high-precision and complex components. We are your reliable partner for the machining of precision components, offering state-of-the-art production facilities for machining, milling, turning and grinding as well as all the necessary measuring technology.
Technological progress is continuously increasing the demands placed on the components used. This results in special materials and alloys with very good technological properties. It is however becoming more and more difficult to process these optimized materials economically.
Komponentenfertigung
Longstanding partnerships
We are proud of the long-standing partnerships with our customers, which we have established and continuously developed. These trusting relationships are the foundation of our success and enable us to offer customized solutions to meet the individual needs of our partners.
Innovative two-table milling machine
Our specifically developed two-table milling machine offers utmost flexibility and efficiency in the processing of components. This ultra-modern machine permits the alternate clamping and processing of two components, which significantly shortens production times and maximizes capacity utilization.
In addition, our milling machine allows for the processing of large parts with impressive dimensions of up to 12,500 mm (length) x 2,200 mm (height) x 3,800 mm (width). This provides you with a wide range of possibilities for complex projects and demanding applications.
Absolute precision in processing
Our expertise in precision machining covers a multitude of materials, including steel, cast iron and mineral castings. We also offer customized solutions for the machining of hybrid components that place the highest demands on precision and surface quality.
Thanks to our progressive milling technology with internal cooling water supply, we not only guarantee optimum cooling during the machining process, but also a significant reduction in deformations and stresses in the material. This results in an outstanding precision and durability of your components.
Manufacturing of large components at the highest level
We manufacture our large parts on a specifically developed CNC portal milling machine, called WORK 300. This very modern machine permits the precise processing of workpieces with impressive dimensions of up to 12,470 mm (length) x 950 mm (height) x 2,900 mm (width).
Thanks to its robust design and advanced technology, the WORK 300 ensures outstanding accuracy and efficiency when processing large components. Whether in the mechanical engineering, automotive or aerospace industry — our solutions are ideally suited for demanding applications where precision and quality have top priority.
5‑axis milling in an air-conditioned environment
With our 5‑axis technology, we are able to mill complex geometries and demanding contours with maximum precision. This is what makes our manufacturing solutions the ideal choice for a wide range of applications.
Thanks to our modern TRIMILL VF3021 portal milling machine, utmost precision and efficiency characterize our parts production. Generous travels of X = 3,000 mm, Y = 2,100 mm and Z = 1,200 mm put us in a position to machine even large-format workpieces with exceptional accuracy.
Furthermore, we use our specifically developed HSM 4020 CNC portal milling machine with angular milling head for parts production. It allows the machining of workpieces with maximum dimensions of 3,760 mm in length, 1,170 mm in height and 2,200 mm in width.
Quality assurance – you can rely on it!
In our air-conditioned quality assurance department, we use the latest technologies to ensure the highest standards in component testing.
Using our high-precision measuring machines of Zeiss and Wenzel make, we are capable of exactly measuring components up to a size of 4,000 mm x 2,000 mm x 1,500 mm. These state-of-the-art systems enable us to detect even the smallest deviations and thereby to ensure that every product meets our strict quality requirements.
Furthermore, we use laser measuring devices in quality control for an even more precise analysis of the components. These devices offer the possibility of efficiently inspecting complex geometries and surface structures, thus ensuring seamless quality assurance. On request, all components will get an individual test report containing detailed information on the measurements carried out and their results.
Picture gallery from our production
Ultramodern paintwork
In our paint shop, we offer a comprehensive service for components up to a size of 12,000 mm. The process includes thorough cleaning, filling, sanding and professional painting of your components.
Heated booths in our paint shop ensure uniform drying and excellent adhesion of the paints and thereby utmost quality and optimum results. Our qualified employees use state-of-the-art technology and high-quality materials to ensure that every component is not only aesthetically pleasing but also durable and robust.
Picture gallery from our production
Machine assembly – manufacturing solutions from a single source
From the manufacture of welded parts to machining and the assembly of components and entire modules – we provide you with everything from a single source. Our holistic approach enables us to efficiently control every step of the production process and guarantee the highest quality standards. Thanks to the close cooperation between the various departments, we guarantee smooth communication and an optimum workflow that saves time and money.
We have mastered the demanding art of scraping machine tables and similar components to meet the highest precision requirements. This traditional technique enables us to process surfaces with exceptional precision and ensure that all components match perfectly.
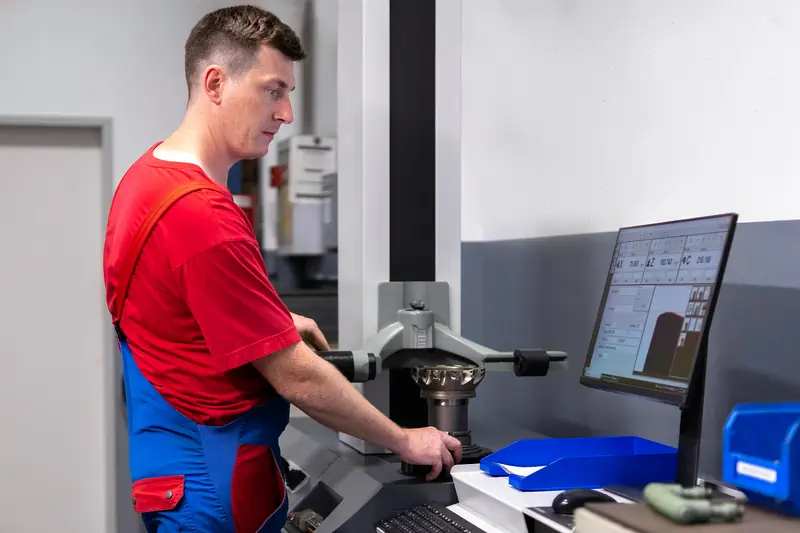
Insight into our tool measurement department
Welcome to our modern tool measurement department! Here we use the latest technologies and precise processes to ensure the quality and accuracy of our tools. Our experienced specialists apply advanced measuring equipment to carefully check and calibrate each tool. This not only guarantees optimum performance, but also compliance with strict quality standards.
Regular training and the use of innovative software solutions enable us to optimize our processes continuously.
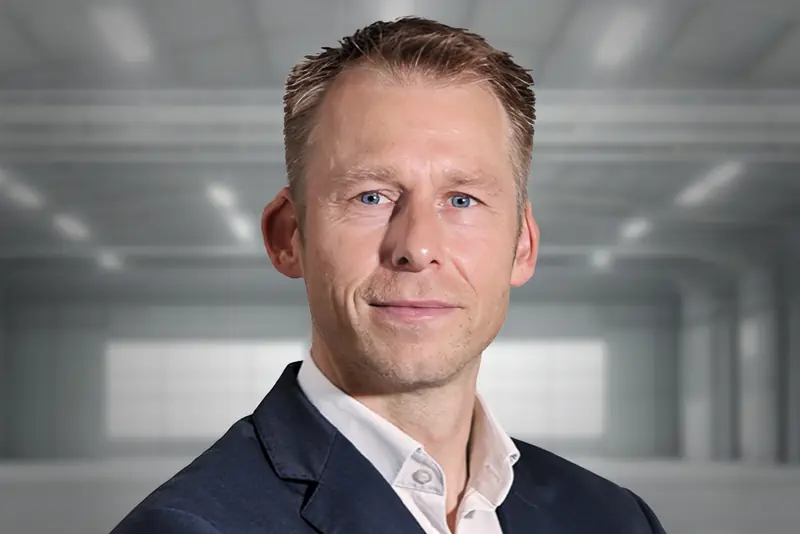
Any questions?
Swen-Uwe Baacke
Component production in Meeder
+49 162 3498167
swen-uwe.baacke@hamuel.de