HybriDX-LT
Hybrid manufacturing technologies
The HybriDX-LT combines industrial 3D printing with precise 5‑axis machining, which can be carried out both during and after the printing process, to ensure maximum accuracy and first-class surface qualities. This system is also ideal for the production of large-volume components, such as façade elements, formwork for the construction industry or casting and pressing molds in mold making. It also enables the efficient and cost-effective production of prototypes as well as small and large series.
HybriDX-LT
Machine variants
ECO-LT basic machine: Low-vibration portal frame with stationary machining table on a stable substructure. A protective cabin including ceiling element encloses the machine completely. Two versions of equipping the unit and a tool changer with 7 places satisfy most diverse customer requirements.
Printing table:
- Table surface heatable up to 150 °C
- Permanent printing plate (surface)
- Base plate from cast aluminium
- Plate milled (level or with grooves)
- Steel bars with fitted and threaded bushes
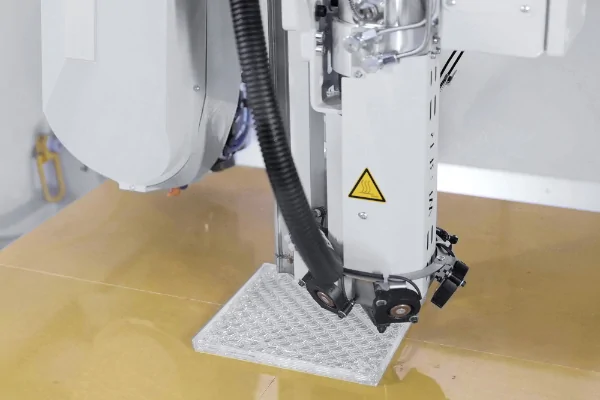
Extruder
- Plasticising up to 450 °C
- Maximum material output from 8 kg/h to 30 kg/h
- Nozzle diameter from 1 mm to 20 mm
- Subsequent to their fusing in the extruder, a nozzle deposits the fused pellets on the build-plate/printing table in layers.

Milling aggregates
The cardanic 5‑axis working head provides for an undercut of up to 46° and can be equipped with different head versions. This permits the high-precision three-dimensional machining of free-form surfaces and contours during and after 3D printing.